Alles ist möglich
Wertschöpfung durch starke Partnerschaften und technische Kompetenz
"Wir müssen unsere Kunden an die erste Stelle setzen. Immer."
Jacques Angst
Eine echte Partnerschaft bedeutet, Synergien mit Ressourcen und Know-how so effizient zu nutzen, dass beide davon profitieren und wachsen können. Wir haben das große Privileg, dies immer wieder zu erleben. Überzeugen Sie sich selbst.
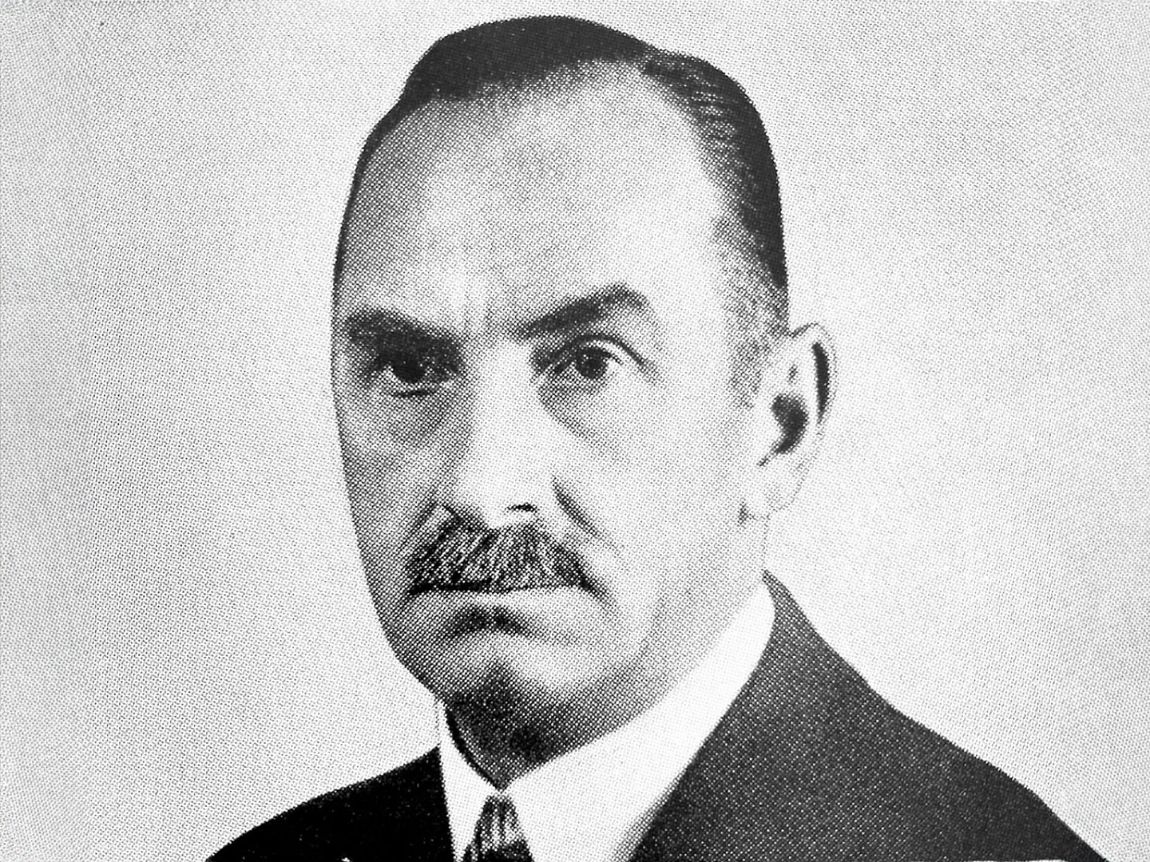
Nachgewiesener Erfolg in Bewegung – Unsere Kundengeschichten
AMZ Racing und Angst+Pfister haben gemeinsam ein innovatives Federungssystem entwickelt.
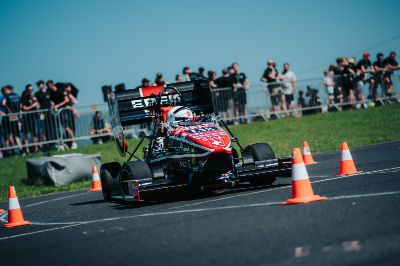
Das EPFL Racing Team und Angst+Pfister haben gemeinsam an der Verbesserung des Formula-Student-Autos gearbeitet.
Der Alphornbauer Bruno Cattaneo und Angst+Pfister haben zusammengearbeitet, um die Montage des Instruments zu verbessern.
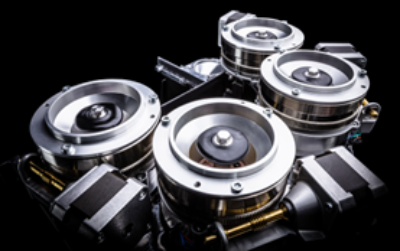
Eversys und Angst+Pfister haben gemeinsam eine kompakte, effiziente Kaffeemahltechnologie entwickelt.
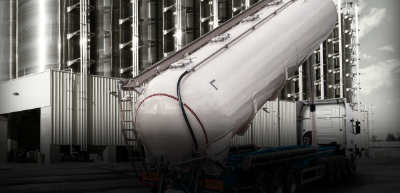
LAG Trailers und Angst+Pfister haben sich zusammengetan, um lebensmittelzugelassene Dichtungslösungen zu verbessern.
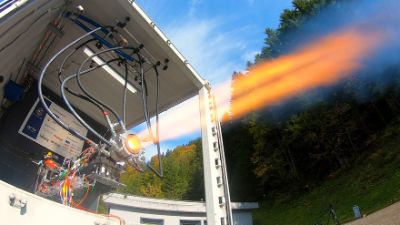
ARIS-Studenten arbeiteten mit Angst+Pfister zusammen, um die kritischen Dichtungslösungen für die Rakete zu entwickeln.
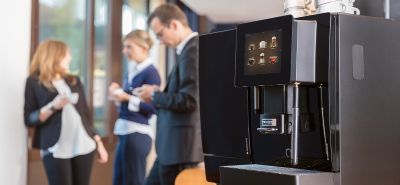
Franke und Angst+Pfister haben gemeinsam platzsparende Dämpfer entwickelt, um die Vibrationen von Kaffeemaschinen zu reduzieren.
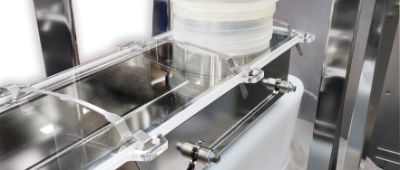
Coperion und Angst+Pfister haben gemeinsam eine kostengünstige, hygienische Silikonhülle entwickelt.
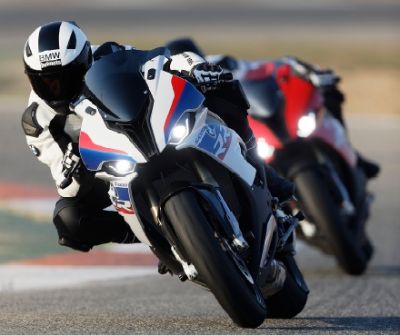.jpg)
Angst+Pfister hat maßgeschneiderte Schwingungsdämpfer für das BMW-Motorrad S 1000 RR entwickelt.
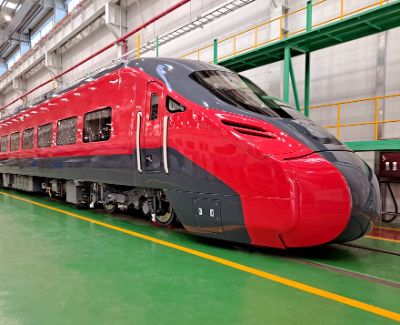
Angst+Pfister arbeitete mit dem südkoreanischen Unternehmen Dawonsys an schwingungsdämpfenden Komponenten zusammen.
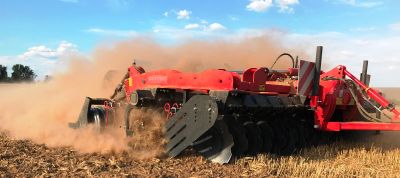
Quivogne und Angst+Pfister haben zusammengearbeitet, um die Haltbarkeit von Scheibeneggen zu verbessern.
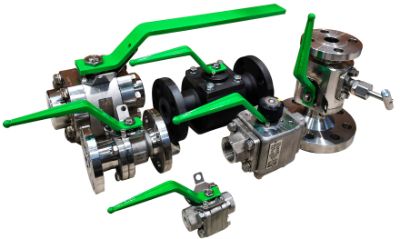
MCM S.p.A. hat in Zusammenarbeit mit Starline wasserstoffbeständige Ventildichtungen entwickelt.
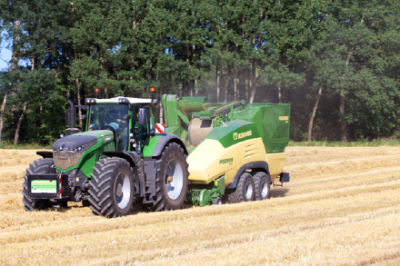
Angst+Pfister entwickelte maßgeschneiderte Dichtungen für die Pellet-Erntemaschinen von Krone.
Wir sorgen dafür, dass es funktioniert!
Nehmen Sie einfach Kontakt mit uns auf und wir werden uns so schnell wie möglich bei Ihnen melden!
Bleiben Sie auf dem Laufenden!
Melden Sie sich noch heute für unseren Newsletter an und erhalten Sie unsere neuesten Informationen über Produkte und Branchentrends!