Avec nous, ça marche !
Des partenariats solides et des capacités d'ingénierie créent de la valeur.
"Nous devons faire passer nos clients en premier. Toujours."
Jacques Angst
Un véritable partenariat consiste à utiliser les synergies avec les ressources et l'expertise de manière si efficace que les deux parties en tirent profit et se développent. Nous avons le grand privilège d'en faire l'expérience à maintes reprises. Voyez par vous-même.
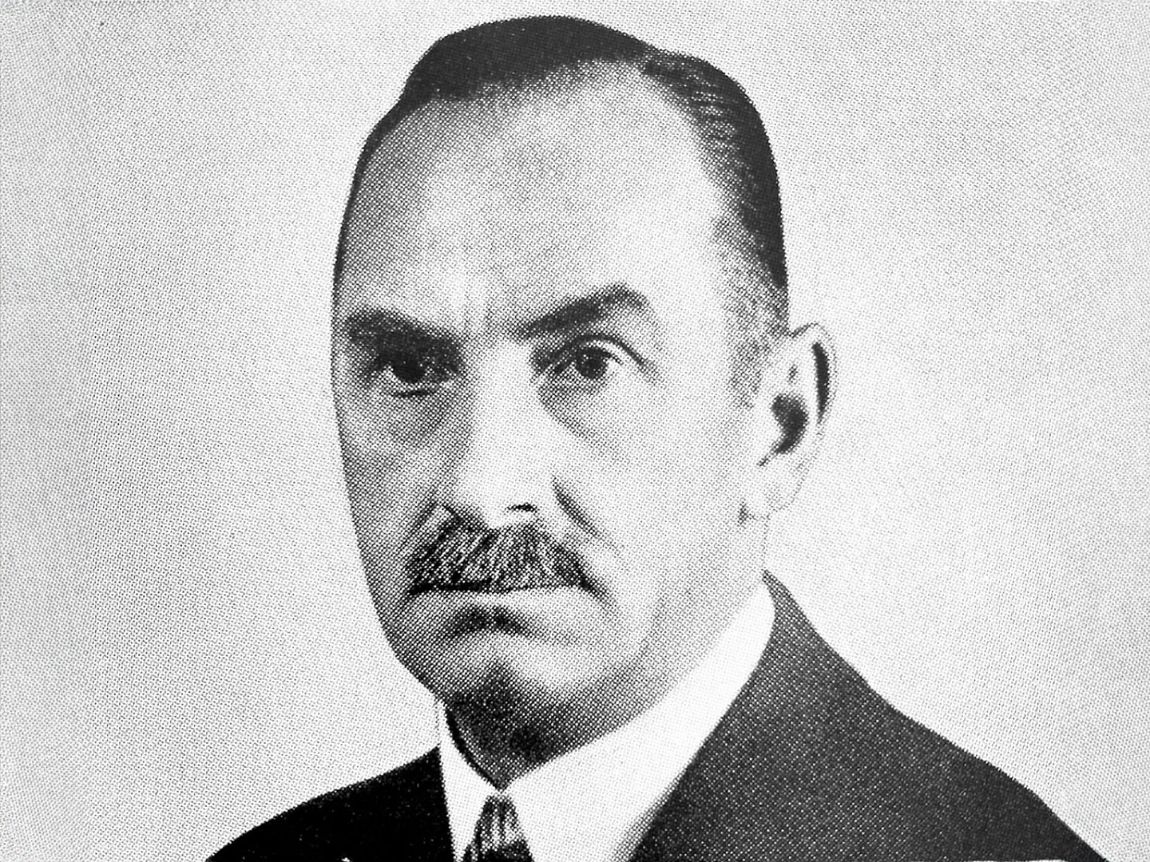
Proven Success in Motion - Nos témoignages de clients
AMZ Racing et Angst+Pfister ont collaboré pour développer un système de suspension innovant.
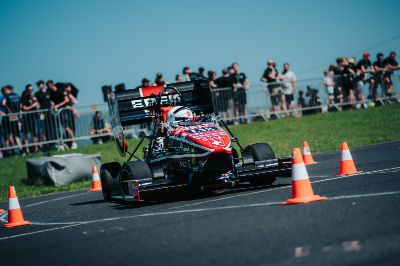
L'équipe de course EPFL et Angst+Pfister ont collaboré pour améliorer la voiture de Formule Student.
Le fabricant de cors des Alpes Bruno Cattaneo et Angst+Pfister ont collaboré pour améliorer l'assemblage de l'instrument.
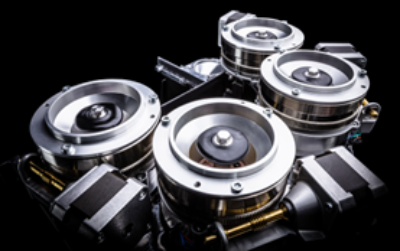
Eversys et Angst+Pfister ont collaboré pour développer une technologie de broyage de café compacte et efficace.
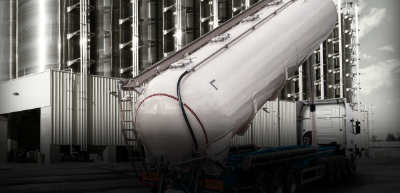
LAG Trailers et Angst+Pfister se sont associés pour améliorer les solutions d'étanchéité approuvées pour les aliments.
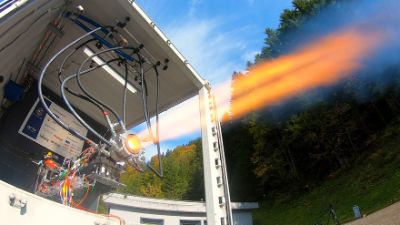
Les étudiants de l'ARIS se sont associés à Angst+Pfister pour les solutions d'étanchéité critiques de la fusée.
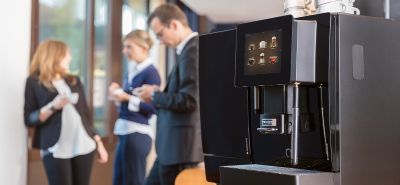
Franke et Angst+Pfister ont développé conjointement des amortisseurs peu encombrants pour réduire les vibrations des machines à café.
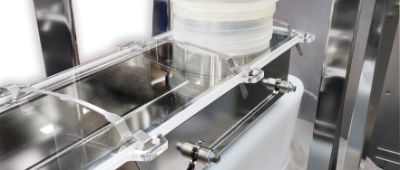
Coperion et Angst+Pfister ont développé conjointement un revêtement en silicone hygiénique et économique.
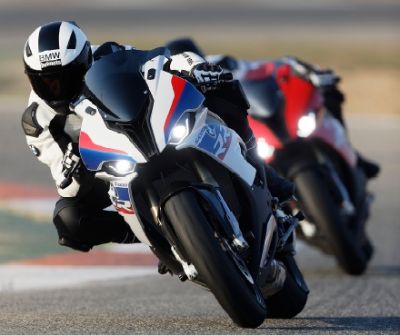.jpg)
Angst+Pfister a conçu des amortisseurs de vibrations sur mesure pour la moto S 1000 RR de BMW.
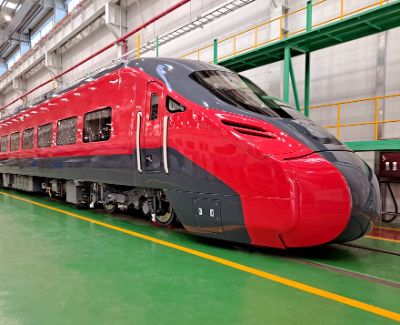
Angst+Pfister a collaboré avec la société sud-coréenne Dawonsys sur des composants antivibratoires.
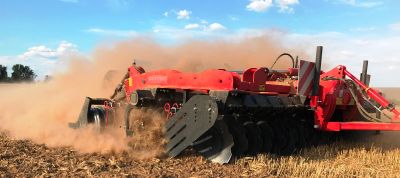
Quivogne et Angst+Pfister ont collaboré pour améliorer la durabilité des déchaumeurs à disques.
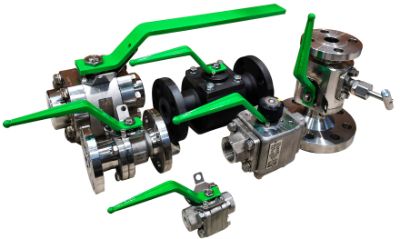
MCM S.p.A a collaboré avec Starline pour développer des joints de soupape résistants à l'hydrogène.
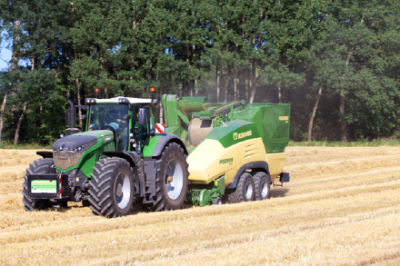
Angst+Pfister a développé des joints sur mesure pour les machines d'extraction de granulés de Krone.
Nous faisons en sorte que vos projets marchent !
Contactez-nous et nous vous répondrons rapidement !
Restez à jour !
Inscrivez-vous dès aujourd'hui à notre lettre d'information et recevez nos dernières mises à jour sur les produits et les dernières tendances de l'industrie !