Wij zorgen dat het werkt!
Sterke partnerschappen en engineeringcapaciteiten creëren waarde.
"We moeten onze klanten op de eerste plaats zetten. Altijd."
Jacques Angst
Een echt partnerschap betekent dat synergieën met middelen en expertise zo efficiënt worden gebruikt dat ze allebei kunnen profiteren en groeien. We hebben het grote voorrecht dit keer op keer te mogen ervaren. Kijk zelf maar.
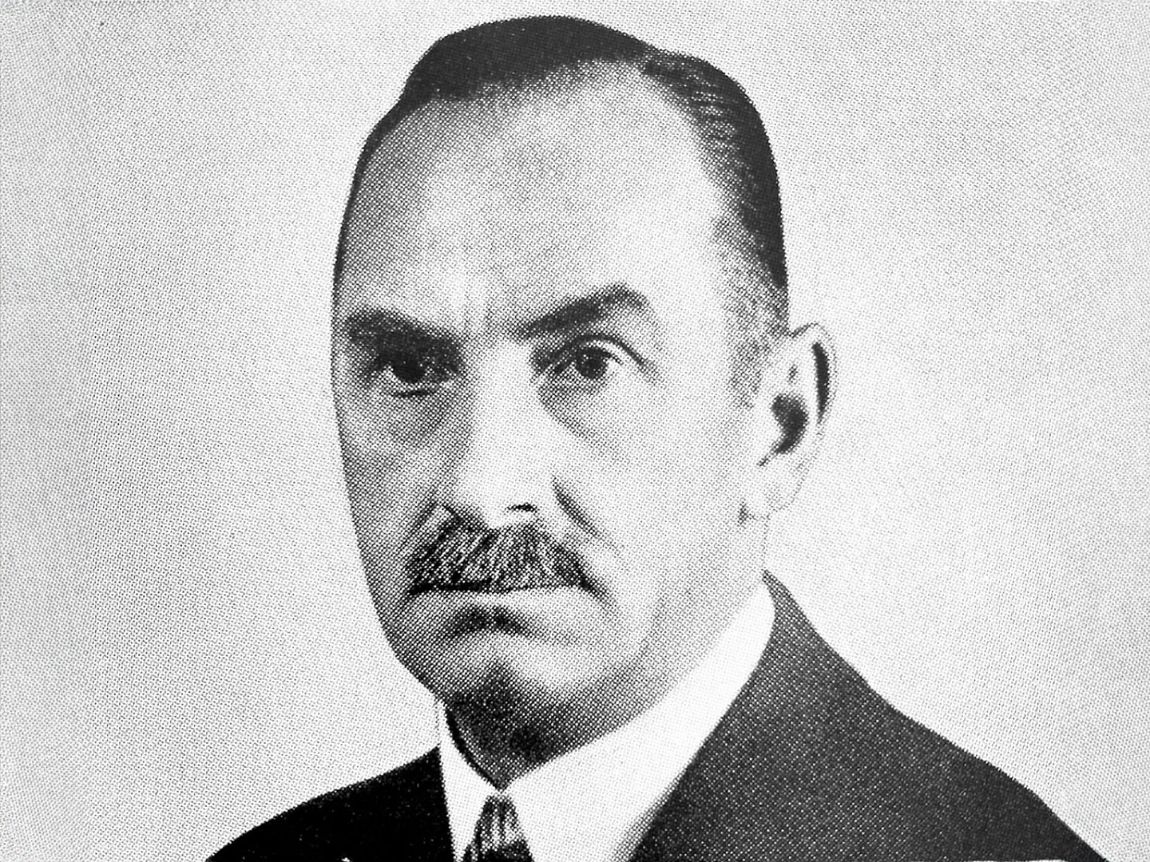
Bewezen succes in beweging - Onze klantverhalen
AMZ Racing en Angst+Pfister hebben samen een innovatief veersysteem ontwikkeld.
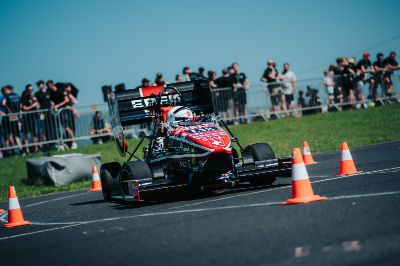
EPFL Racing Team en Angst+Pfister hebben samengewerkt om de Formula Student auto te verbeteren.
Alfhoornbouwer Bruno Cattaneo en Angst+Pfister hebben samengewerkt om de assemblage van het instrument te verbeteren.
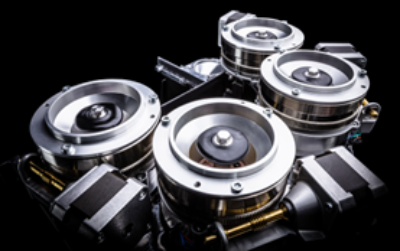
Eversys en Angst+Pfister hebben samengewerkt om een compacte, efficiënte koffiemalingstechnologie te ontwikkelen.
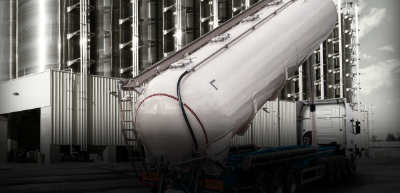
LAG Trailers en Angst+Pfister werken samen om de afdichtingsoplossingen te verbeteren die goedgekeurd zijn voor levensmiddelen.
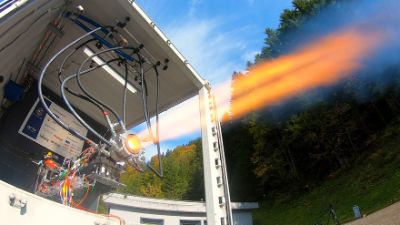
ARIS-studenten werken samen met Angst+Pfister voor cruciale afdichtingsoplossingen voor raketten.
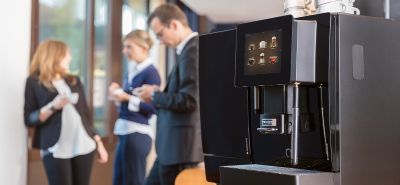
Franke en Angst+Pfister hebben samen ruimtebesparende dempers ontwikkeld om de trillingen van koffiemachines te verminderen.
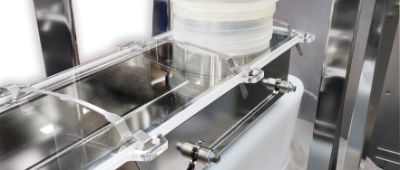
Coperion en Angst+Pfister hebben samen een kosteneffectieve, hygiënische siliconen afdekking ontwikkeld.
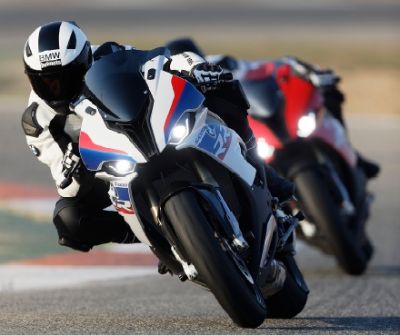.jpg)
Angst+Pfister engineered custom vibration dampers for BMW's S 1000 RR motorcycle.
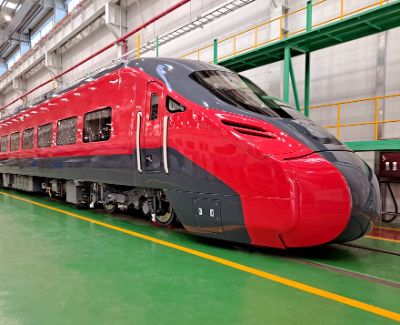
Angst+Pfister werkte samen met het Zuid-Koreaanse Dawonsys aan trillingdempende componenten.
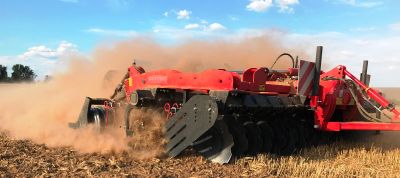
Quivogne en Angst+Pfister hebben samengewerkt om de duurzaamheid van schijveneggen te verbeteren.
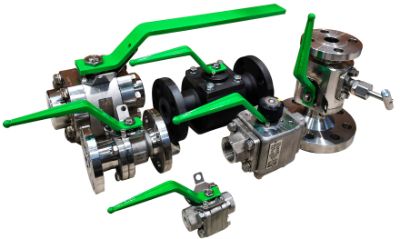
MCM S.p.A werkte samen met Starline om waterstofbestendige klepafdichtingen te ontwikkelen.
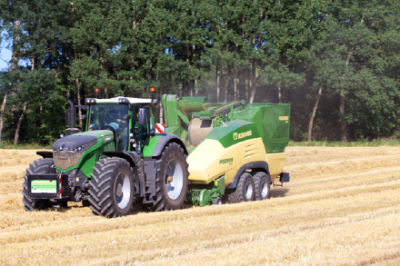
Angst+Pfister ontwikkelde aangepaste afdichtingen voor de pelletoogstmachines van Krone.
Wij zorgen dat het werkt
Neem gewoon contact met ons op en we nemen snel contact met u op!
Blijf op de hoogte!
Meld u vandaag nog aan voor onze nieuwsbrief en ontvang onze nieuwste updates over producten en de laatste trends in de branche!