İşe yaramasını sağlıyoruz!
Güçlü ortaklıklar ve mühendislik yetenekleri değer yaratır.
"Müşterilerimize öncelik vermeliyiz. Her zaman."
Jacques Angst
Gerçek bir ortaklık, kaynakların ve uzmanlığın sinerjisini her ikisinin de faydalanabileceği ve büyüyebileceği kadar verimli kullanmak anlamına gelir. Bunu defalarca deneyimleme ayrıcalığına sahibiz. Kendiniz görün.
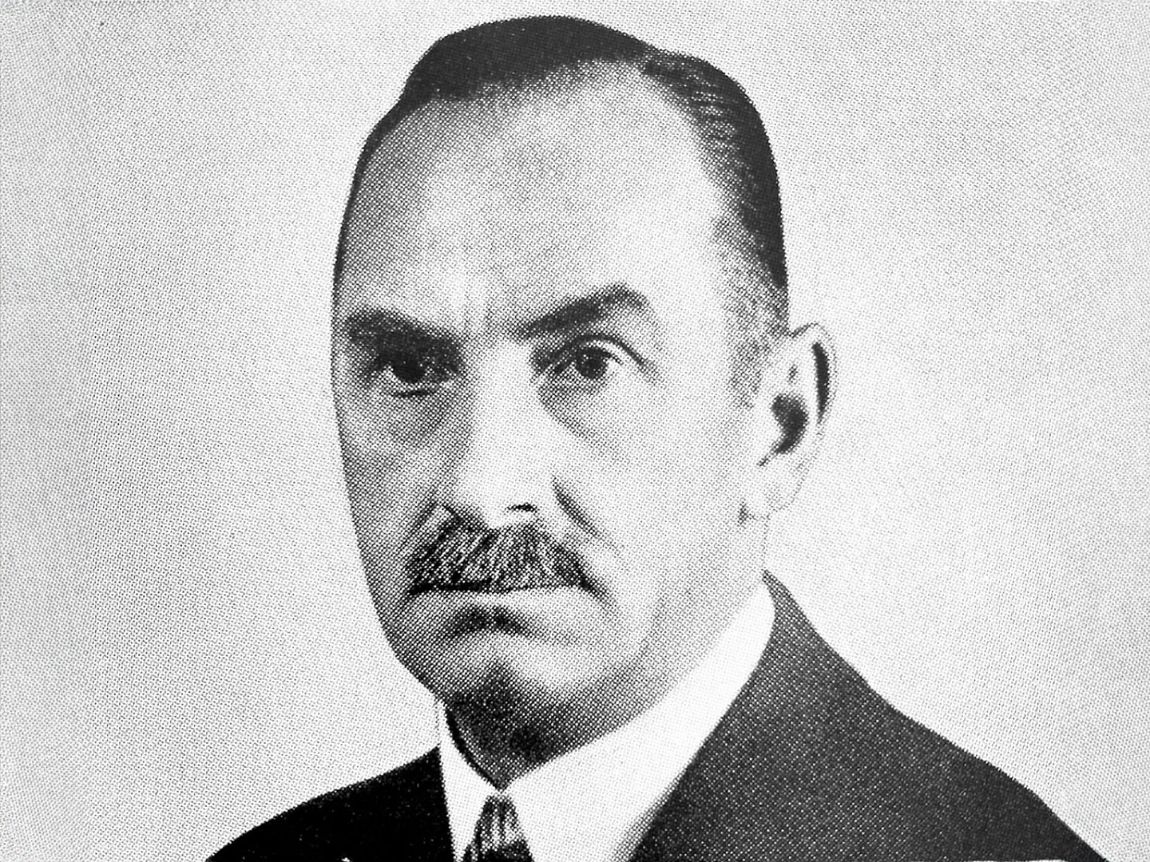
Hareket Halinde Kanıtlanmış Başarı - Müşteri Hikayelerimiz
AMZ Racing ve Angst+Pfister yenilikçi bir süspansiyon sistemi geliştirmek için işbirliği yaptı.
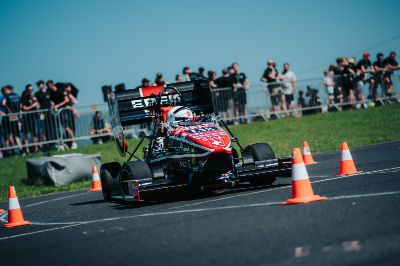
EPFL Racing Team ve Angst+Pfister Formula Student aracını geliştirmek için işbirliği yaptı.
Alforno üreticisi Bruno Cattaneo ve Angst+Pfister, enstrümanın montajını geliştirmek için işbirliği yaptı.
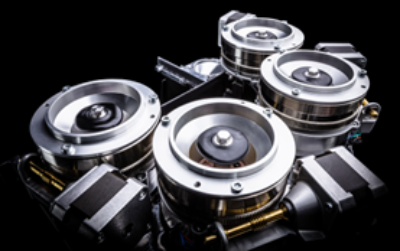
Eversys ve Angst+Pfister kompakt, verimli kahve öğütme teknolojisi geliştirmek için işbirliği yaptı.
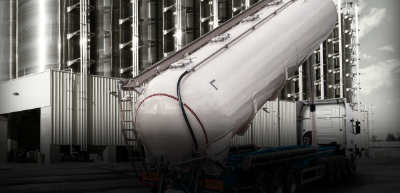
LAG Trailers ve Angst+Pfister gıda onaylı sızdırmazlık çözümlerini geliştirmek için ortaklık kurdu.
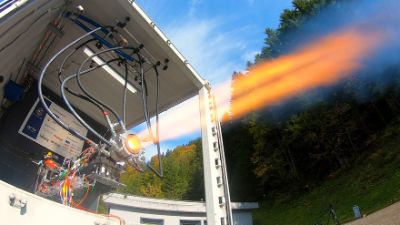
ARIS öğrencileri roketin kritik sızdırmazlık çözümleri için Angst+Pfister ile ortaklık kurdu.
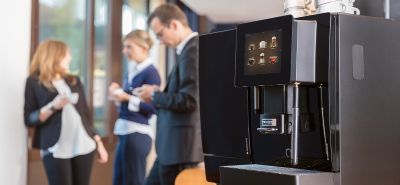
Franke ve Angst+Pfister, kahve makinesi titreşimlerini azaltmak için yerden tasarruf sağlayan damperleri birlikte geliştirdi.
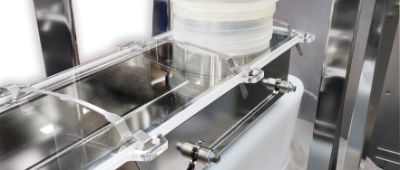
Coperion ve Angst+Pfister birlikte uygun maliyetli, hijyenik bir silikon kapak geliştirdi.
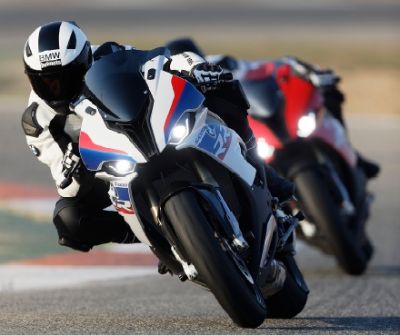.jpg)
Angst+Pfister, BMW'nin S 1000 RR motosikleti için özel titreşim damperleri tasarladı.
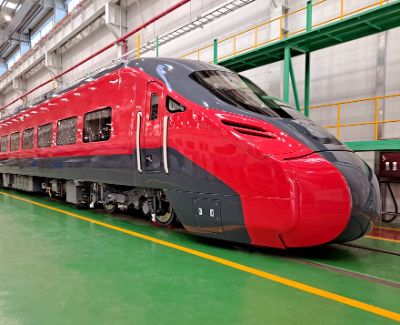
Angst+Pfister, titreşim önleyici bileşenler konusunda Güney Koreli Dawonsys ile işbirliği yaptı.
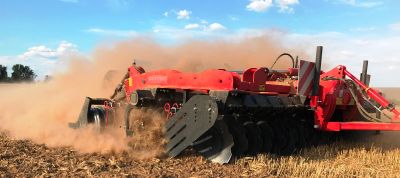
Quivogne ve Angst+Pfister diskli tırmık dayanıklılığını artırmak için işbirliği yaptı.
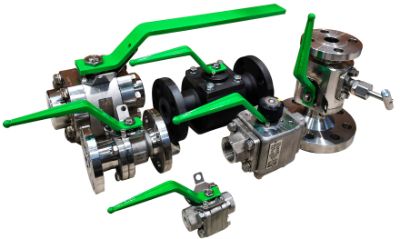
MCM S.p.A, hidrojene dayanıklı valf contaları geliştirmek için Starline ile işbirliği yaptı.
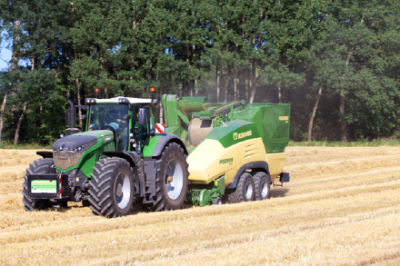
Angst+Pfister, Krone'nin pelet hasat makineleri için özel contalar geliştirdi.
İşe yaramasını sağlıyoruz!
Sadece bizimle iletişime geçin ve size hızlı bir şekilde geri dönelim!
Güncel kalın!
Bugün bültenimize kaydolun ve ürünler ve en son endüstri trendleri hakkındaki en yeni güncellemelerimizi alın!