我们让它发挥作用!
强大的合作伙伴关系和工程能力就能创造价值
"我们的理念是客户至上"。
Jacques Angst
真正的合作伙伴关系是有效利用资源和专业知识的共同合作,使双方都能受益和发展。我们有幸一次又一次地体会到这一点。
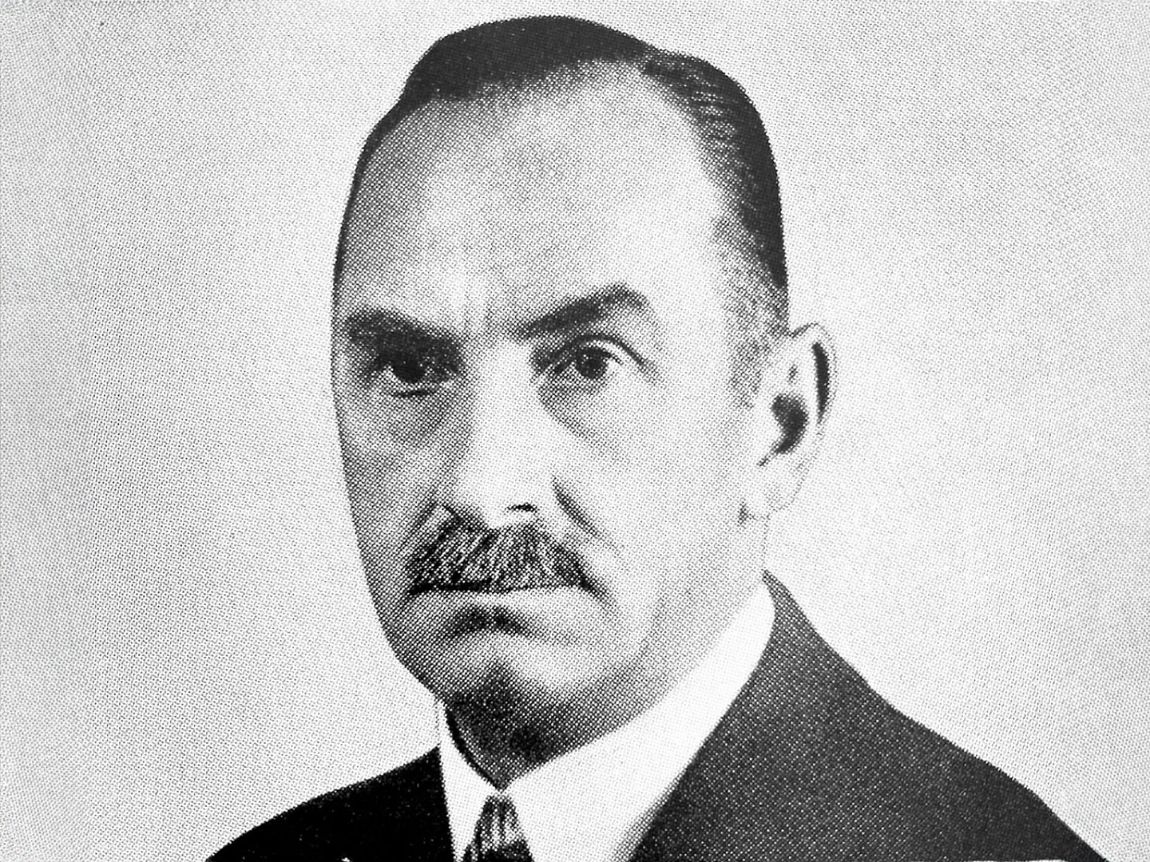
久经考验的成功案例——我们的客户故事
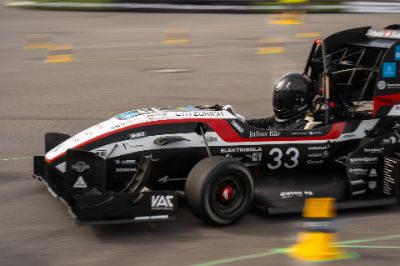
AMZ Racing和昂思菲特(Angst+Pfister)合作开发了一种创新的悬挂系统。
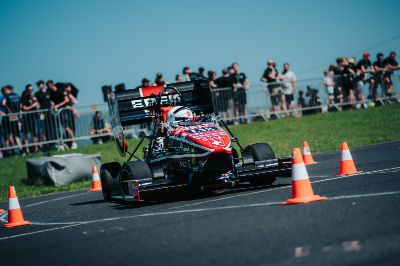
洛桑联邦理工学院赛车队和昂思菲特公司合作,共同改进了大学生方程式赛车。
阿尔卑斯长号制造商布鲁诺·卡塔内奥(Bruno Cattaneo)与昂思菲特(Angst+Pfister)合作,共同改进乐器的组装工艺。
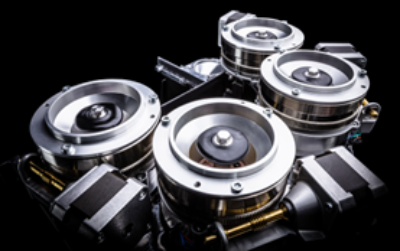
Eversys和昂思菲特(Angst+Pfister)合作开发了紧凑高效的咖啡研磨技术。
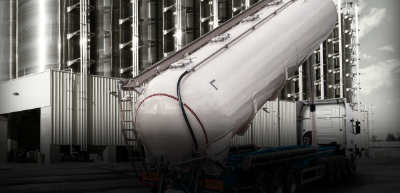
LAG拖车和昂思菲特公司合作,共同开发食品级密封解决方案。
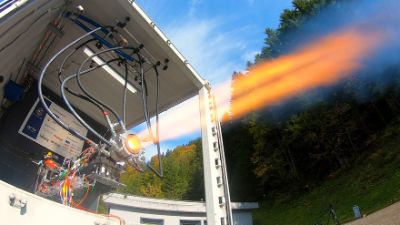
ARIS的学生与昂思菲特公司合作,为火箭提供关键的密封解决方案。
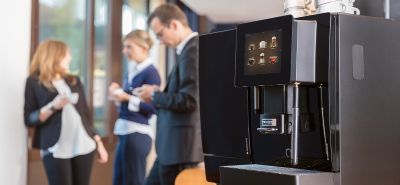
Franke和Angst+Pfister共同开发了节省空间的减震器,以减少咖啡机的振动。
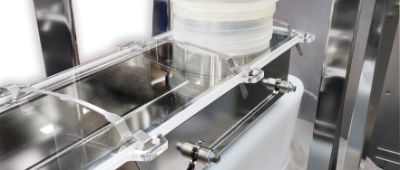
科倍隆和昂思菲特共同开发了一种经济、卫生的硅胶盖。
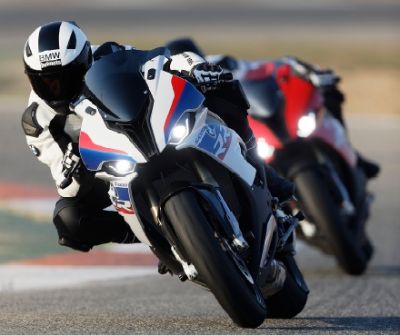.jpg)
昂思菲特为宝马S 1000 RR摩托车设计了定制减震器。
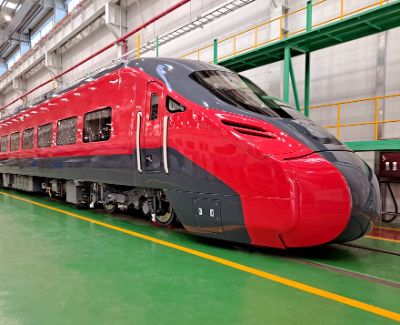
昂思菲特与韩国Dawonsys公司合作开发防震部件。
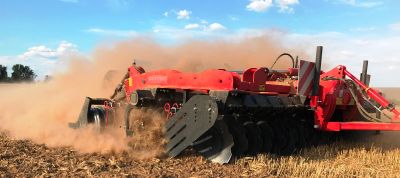
Quivogne和昂思菲特公司合作,共同提高圆盘耙的耐用性。
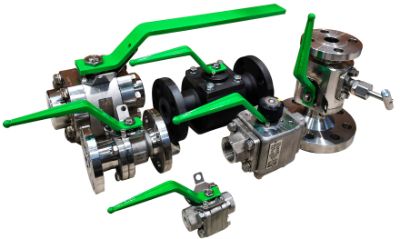
MCM S.p.A公司与Starline公司合作开发耐氢阀门密封件。
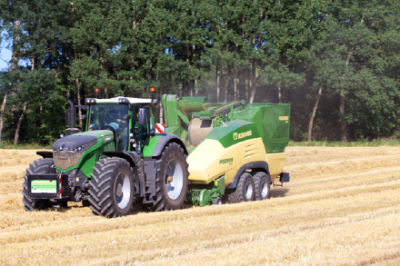
昂思菲特为克朗的颗粒收割机开发了定制密封件。
我们让它发挥作用!
请联系我们,我们会尽快给您回复!
了解最新信息!
今天就注册我们的时事通讯,接收我们最新的产品信息和最新的行业趋势!