
欢迎访问Angst+Pfister Solutions Hub - 我们的工程博客和获取机械与工业工程专家见解的门户。
Angst+Pfister 专注于为客户量身定制高性能密封、防震和流体处理的工业工程解决方案。凭借一个多世纪的丰富经验,我们通过专业技术和创新材料,帮助各行各业的工程师解决复杂的难题。
解决方案中心是我们为工程师和专业技术人员提供的知识平台。在这里,您可以找到有关最新行业主题的深度内容--从不含 PFAS 的创新和法规更新,到智能弹性体和可持续解决方案(如生物基塑料)。
通过应用工程案例研究、法规简报和真实案例,解决方案中心提供实用的知识和行之有效的策略,帮助工程师和技术专业人员应对复杂的挑战。查看我们的 “本月趋势 - 解决方案中心亮点”,了解各行业的创新驱动力,或浏览我们的所有博文。
不要再错过任何行业热门话题或专家见解。
本月趋势 - 我们的 SolutionsHub 亮点
浏览我们的博客文章
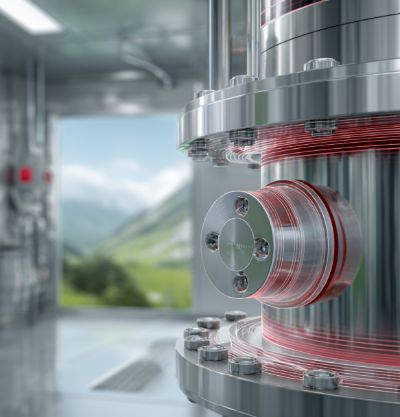
evolast® FFKM 具有极强的耐受性,完全符合欧洲标准,可防止密封失效。
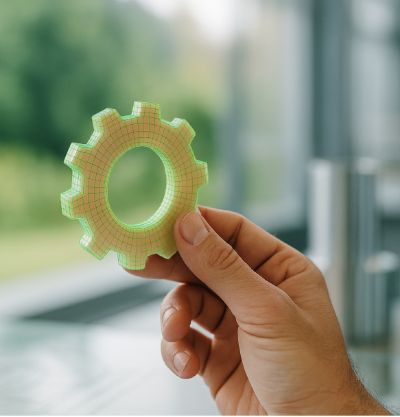
了解塑料如何减少二氧化碳排放并保持良好性能
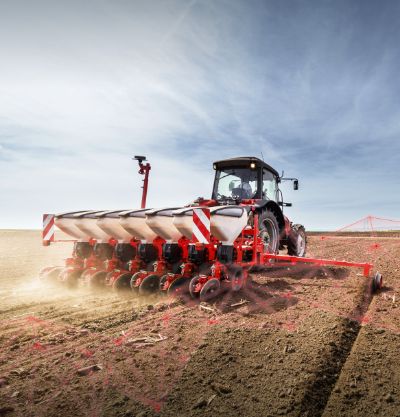
探索盒式密封如何为动力传动系统提供持久保障与高效性能
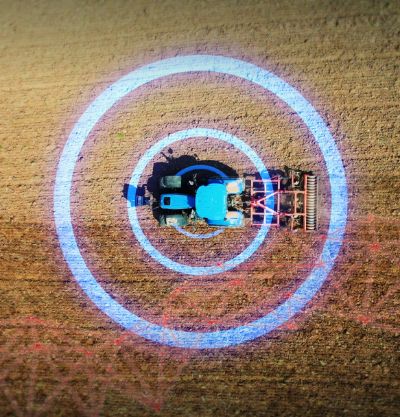
智能弹性体实现实时监控、预测性维护和效率提升。
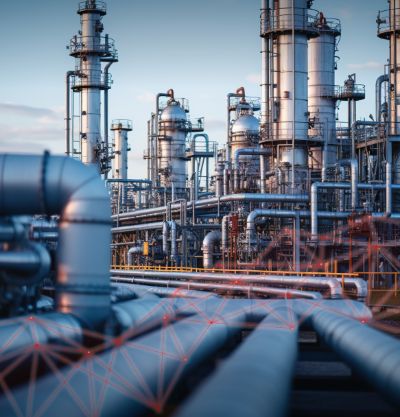
使用寿命最长的不锈钢波纹软管,安全高效地操作液化天然气系统
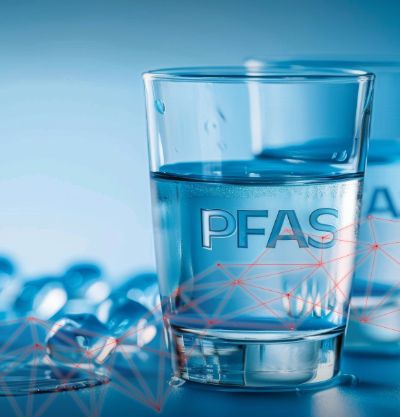
欧盟提议的PFAS法规可能会对聚合物密封材料产生影响。欧洲化学品管理局(ECHA)承认含氟聚合物在密封技术中的重要性。不含PFAS的替代品正在开发中。全面禁止可能会导致密封件使用寿命缩短。
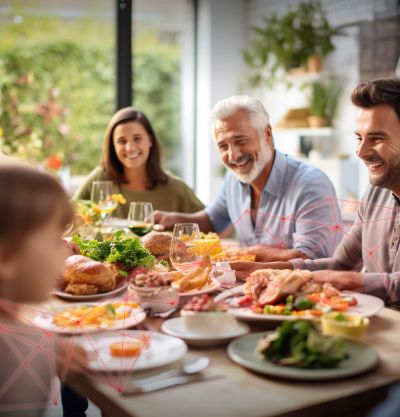
对于中型原始设备制造商而言,如何应对食品和饮料行业中安全、经济高效的塑料部件所带来的挑战,对于在保持经济效益的同时满足严格的合规性要求至关重要。
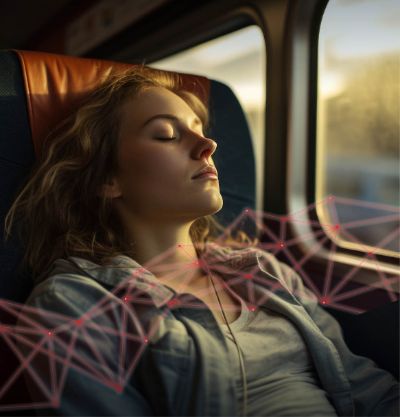
Angst+Pfister 为满足 EN45545 防火标准提供了有效的解决方案。
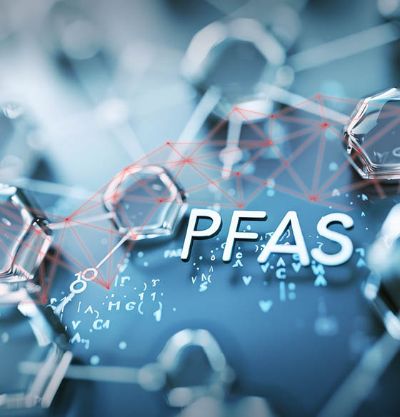
新的全球 PFAS 法规推动使用不含 PFAS 的材料,敦促与可信赖的供应商合作
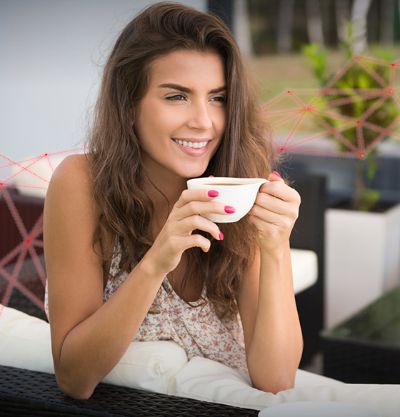
The choice of the optimum material guarantees unlimited coffee enjoyment.
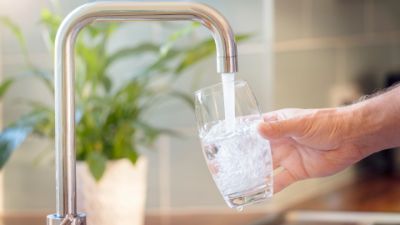
昂思菲特的HITEC® DW三元乙丙橡胶弹性体符合并超越了即将出台的KTW-BWGL饮用水标准,确保卓越的合规性。
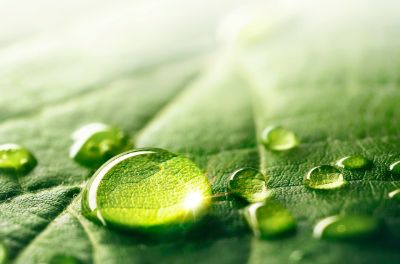
昂思菲特的PERTEC® UP三元乙丙橡胶复合物符合全球食品接触法规,确保密封件安全合规。
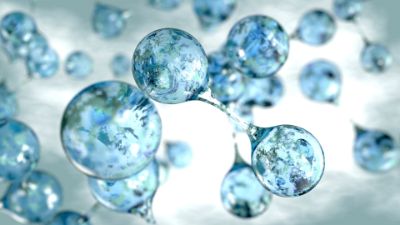
昂思菲特公司严格测试氢气应用中的弹性体,确保其适用于未来的能源解决方案。
我们让它发挥作用!
请联系我们,我们会尽快给您回复!
了解最新信息!
今天就注册我们的时事通讯,接收我们最新的产品信息和最新的行业趋势!