Sprawiamy, że to działa!
Silne partnerstwa i możliwości inżynieryjne tworzą wartość.
„Musimy stawiać naszych klientów na pierwszym miejscu. Zawsze."
Jacques Angst
Prawdziwe partnerstwo oznacza wykorzystanie synergii zasobów i wiedzy specjalistycznej w sposób tak efektywny, że obie strony mogą odnieść korzyści i rozwijać się. Mamy ogromny przywilej doświadczać tego raz po raz. Sam zobacz.
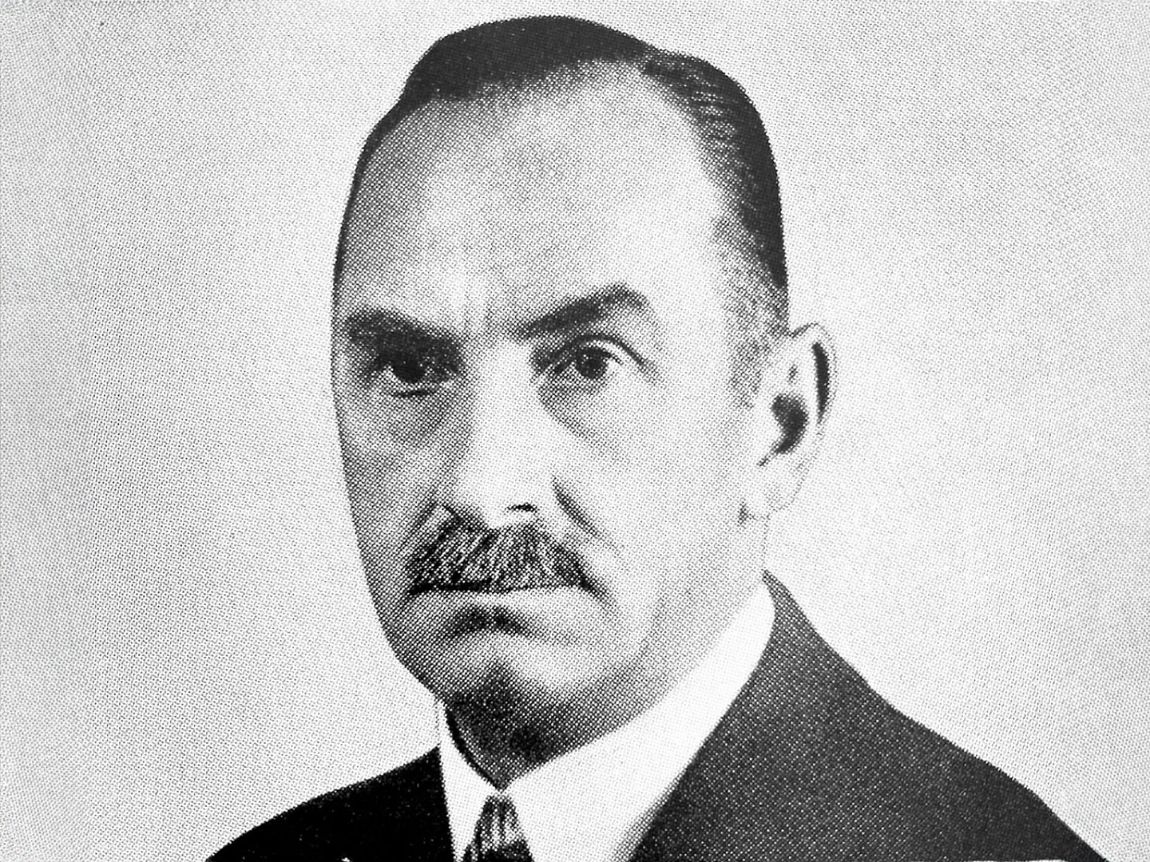
Sprawdzony sukces w ruchu - historie naszych klientów
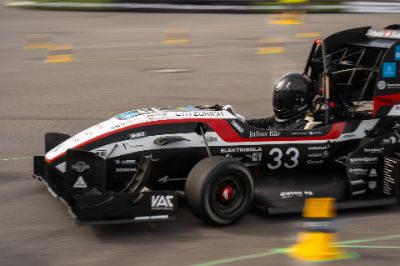
AMZ Racing i Angst+Pfister współpracowały w celu opracowania innowacyjnego systemu zawieszenia.
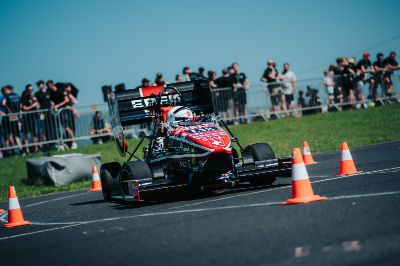
EPFL Racing Team i Angst+Pfister współpracowały nad ulepszeniem bolidu Formuły Student.
Producent alphornów Bruno Cattaneo i Angst+Pfister współpracowali w celu ulepszenia montażu instrumentu.
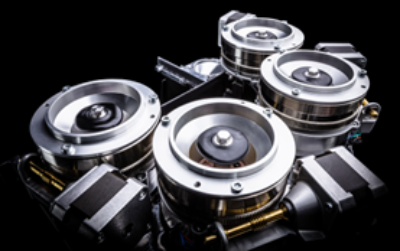
Firmy Eversys i Angst+Pfister podjęły współpracę w celu opracowania kompaktowej i wydajnej technologii mielenia kawy.
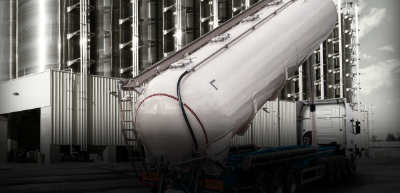
Firmy LAG Trailers i Angst+Pfister nawiązały współpracę w celu ulepszenia rozwiązań uszczelniających dopuszczonych do kontaktu z żywnością.
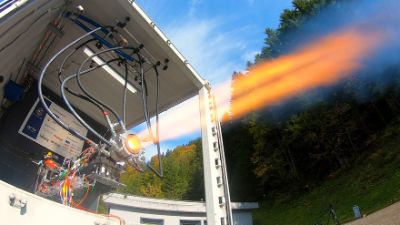
Studenci ARIS nawiązali współpracę z firmą Angst+Pfister w zakresie krytycznych rozwiązań uszczelniających dla rakiet.
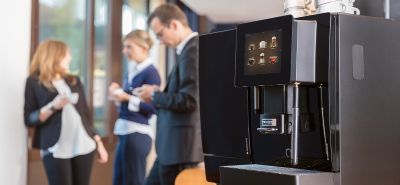
Firmy Franke i Angst+Pfister wspólnie opracowały zajmujące niewiele miejsca amortyzatory redukujące drgania ekspresów do kawy.
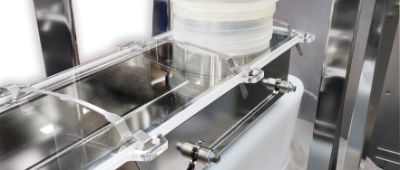
Firmy Coperion i Angst+Pfister wspólnie opracowały ekonomiczną, higieniczną osłonę silikonową.
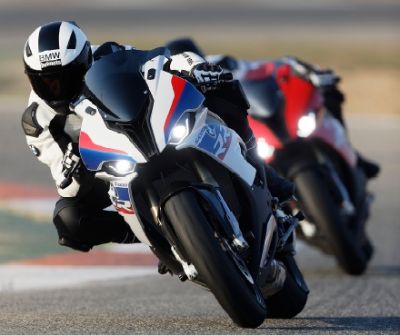.jpg)
Angst+Pfister engineered custom vibration dampers for BMW's S 1000 RR motorcycle.
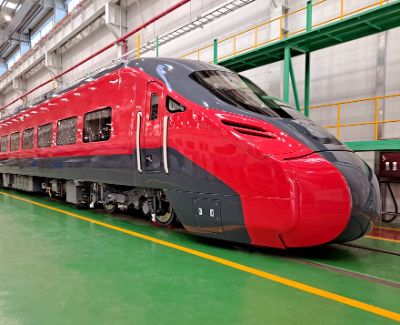
Angst+Pfister współpracował z południowokoreańską firmą Dawonsys nad komponentami antywibracyjnymi.
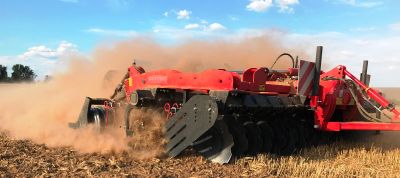
Firmy Quivogne i Angst+Pfister podjęły współpracę w celu zwiększenia trwałości bron talerzowych.
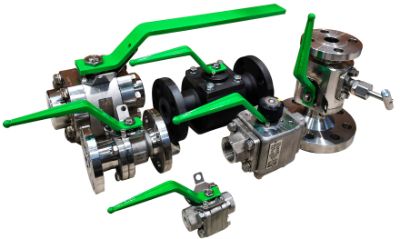
MCM S.p.A współpracowała z firmą Starline w celu opracowania wodoroodpornych uszczelek zaworów.
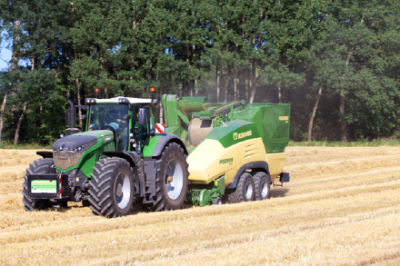
Firma Angst+Pfister opracowała niestandardowe uszczelnienia dla maszyn do zbioru peletów firmy Krone.
Sprawiamy, że to działa!
Po prostu skontaktuj się z nami, a my szybko Tobie odpowiemy!
Bądź na bieżąco!
Zapisz się do naszego newslettera już dziś i otrzymuj najnowsze informacje o produktach i trendach w branży!