A Cornerstone of Reliability
Our O-Ring Solutions.
Our O-Ring assortment is meticulously curated to offer high-performance elastomers and materials. They ensure superior sealing performance at an exceptional price-performance ratio. Our solutions cater to a wide array of industries, including Food and Beverage, Process, Medical, and Chemical. They provide unmatched reliability and durability in every application.
Contact us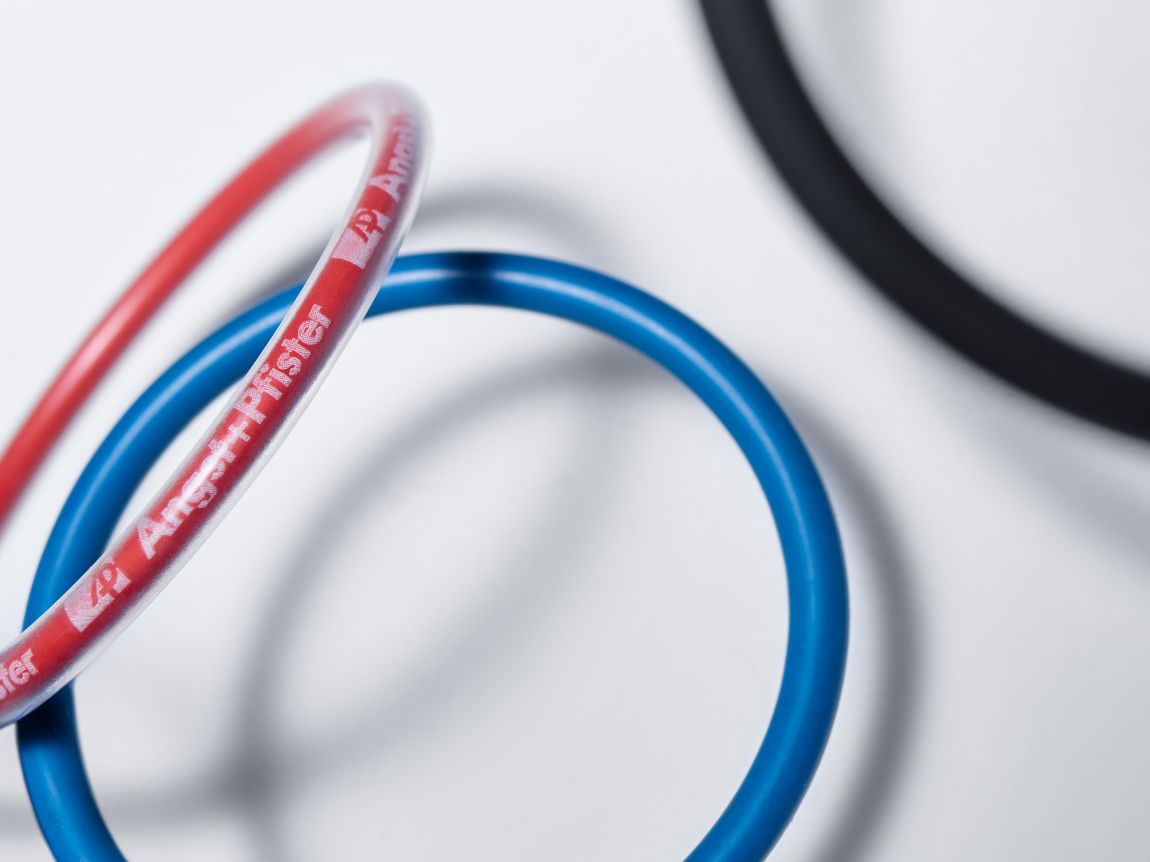
Precision Tailored to Your Needs
Custom Molded Parts.
Experience the power of precision with our custom molded parts and rubber seals. Crafted to meet your exact requirements, these customized components offer significant advantages over standard seals. Our molded seals are designed for specific deployment purposes and tailored to fit your equipment or part design precisely. They ensure optimal functionality and maximum leak-tightness. Our custom solutions are engineered to excel in the most challenging environments using materials that range from NBR to FFKM.
Contact us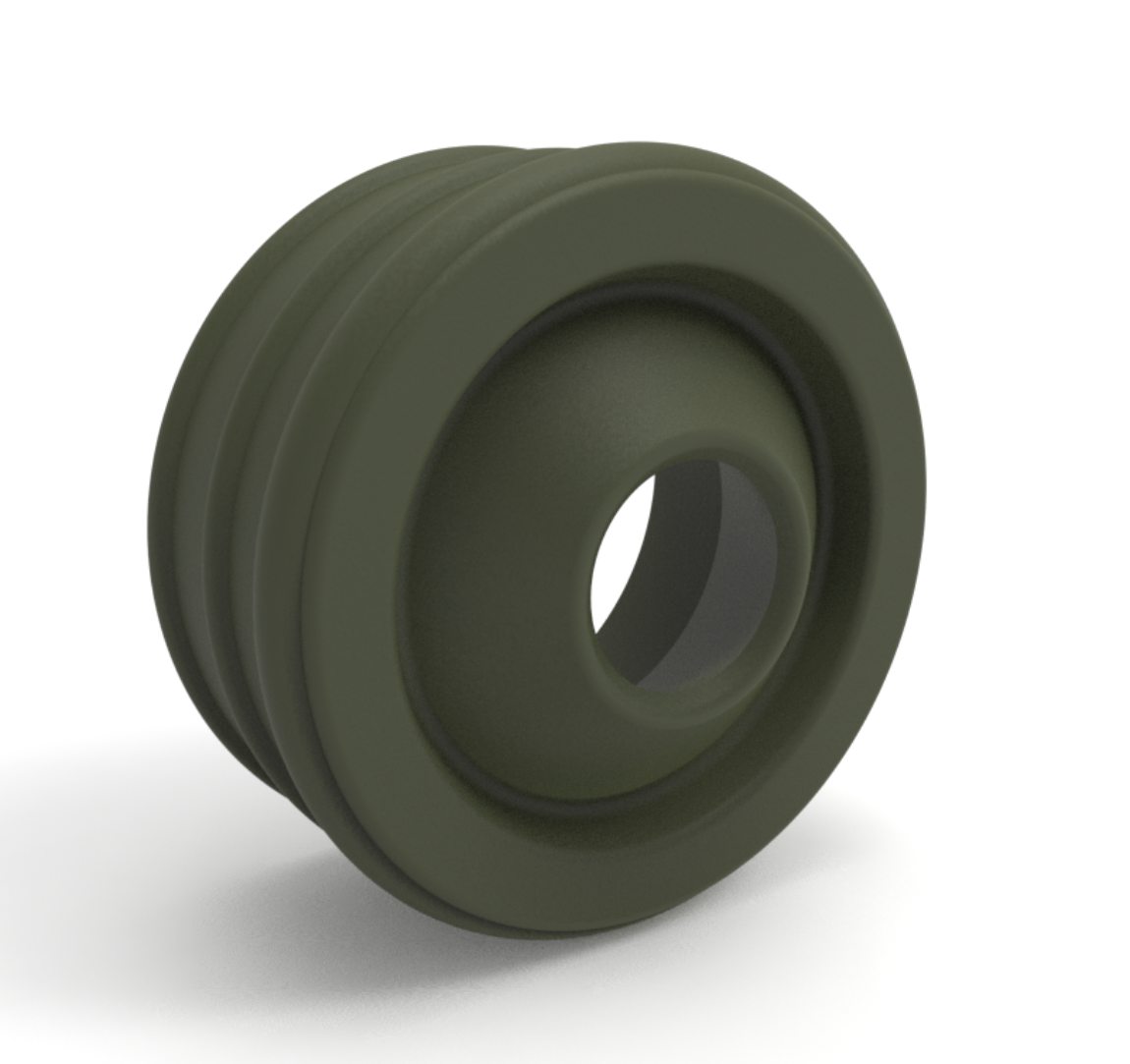
Innovation at Your Fingertips
Materials Matter.
Stay ahead of the curve with our cutting-edge elastomeric materials, engineered to address the evolving needs of modern industries. We empower you to push the boundaries of sealing performance with a broad range of compounds including evolast®, FFKM, FKM, EPDM, HNBR, VMQ, and PTFE.
Download our compound table for in-depth information about our performance compounds product range.
Download now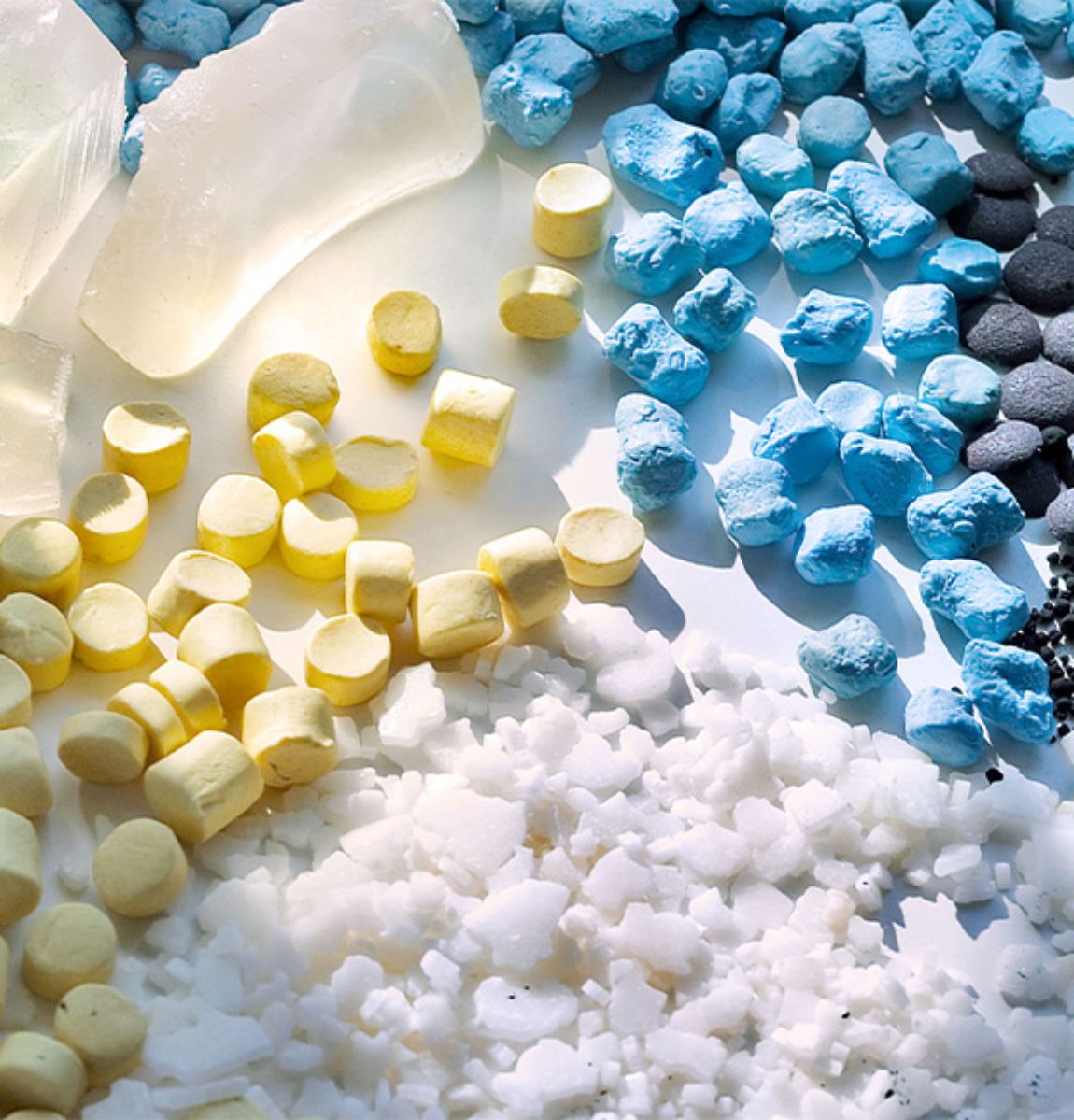
evolast® FFKM Sealing Solutions
100% Developed, Compounded, and Manufactured In-house in Europe.
We engineered evolast® for critical applications in Chemical Processing, Pharma, MedTech, Semiconductors, and Energy. evolast® withstands extreme temperatures up to +340 °C and a wider range of aggressive chemicals than conventional elastomers. It ensures high precision, durability, and consistent performance.
Our solutions include O-Rings, Molded Parts, and Plates — designed, tested, and validated according to your specific needs.
Download now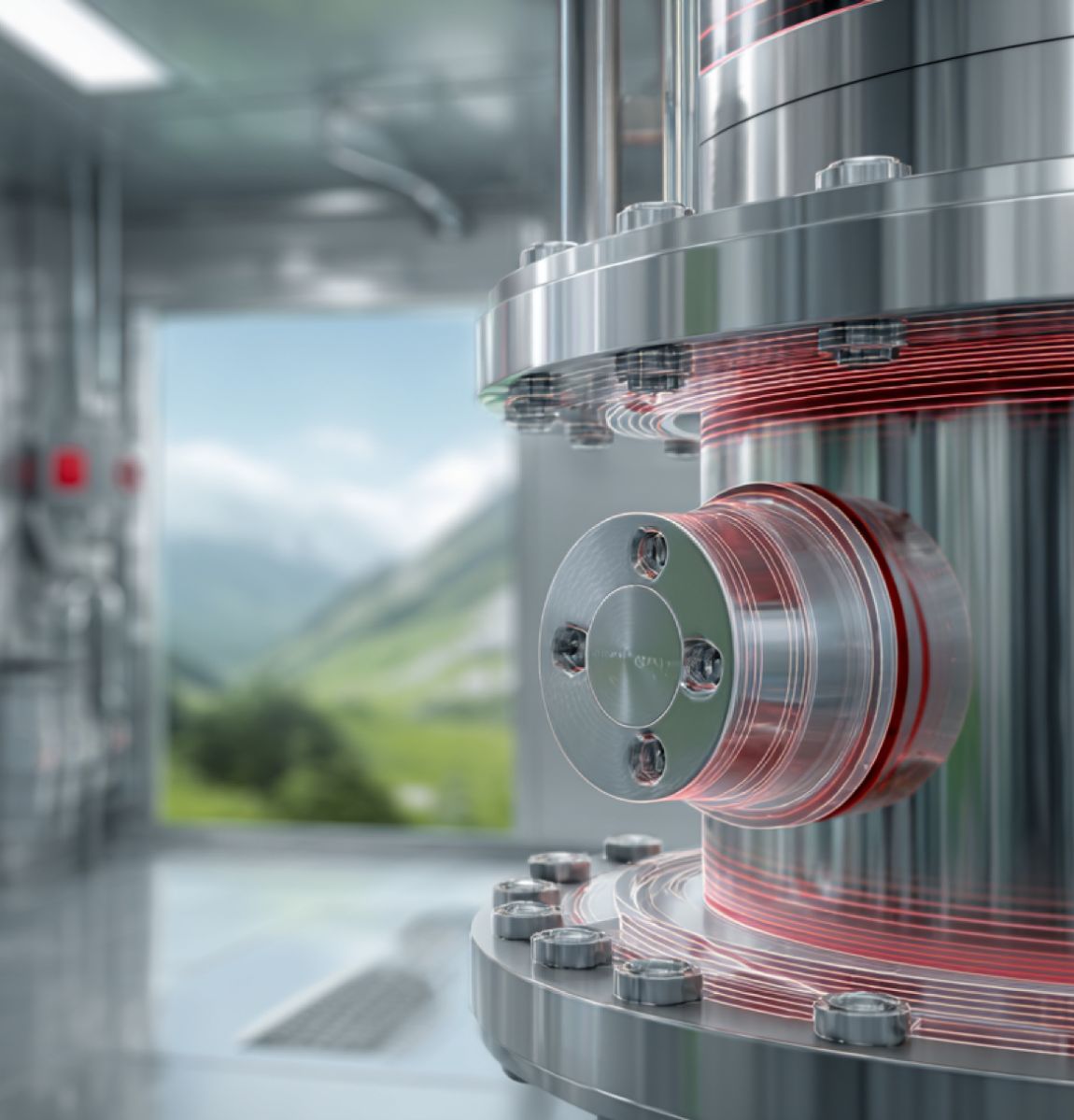
Which industry are you in?
Our Key Industries for O-Ring and Molded Solutions
Let’s Talk about your Project!
Request a Free Consultation and Find a Perfect Solution Customized for you.
Based on our assortment we create and develop an individual solution for your application – or we even develop from scratch a high-performance part for your product to ensure quality & safety. For expert advice and customized solutions tailored to your specific needs, Angst+Pfister service offerings are your go-to resource in o-ring and molded parts solutions.
Let's talk!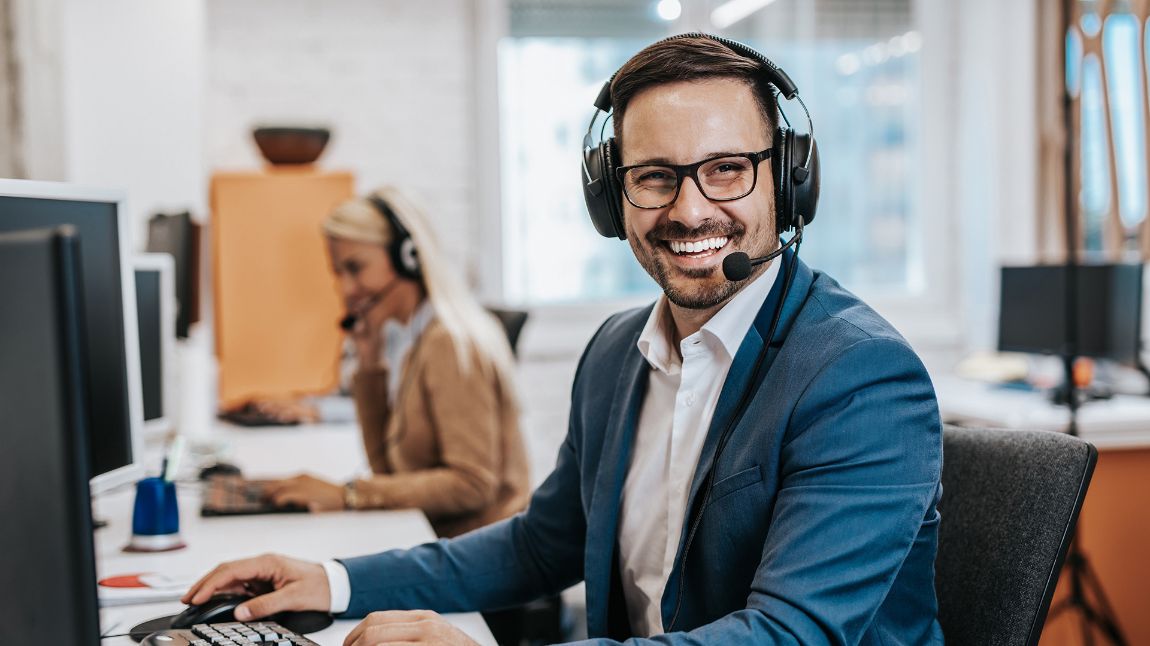
Your Complimentary Technical Guide Awaits
Further explore the world of O-Rings and Molded Solutions through our complimentary technical guides. Download the guides for free.
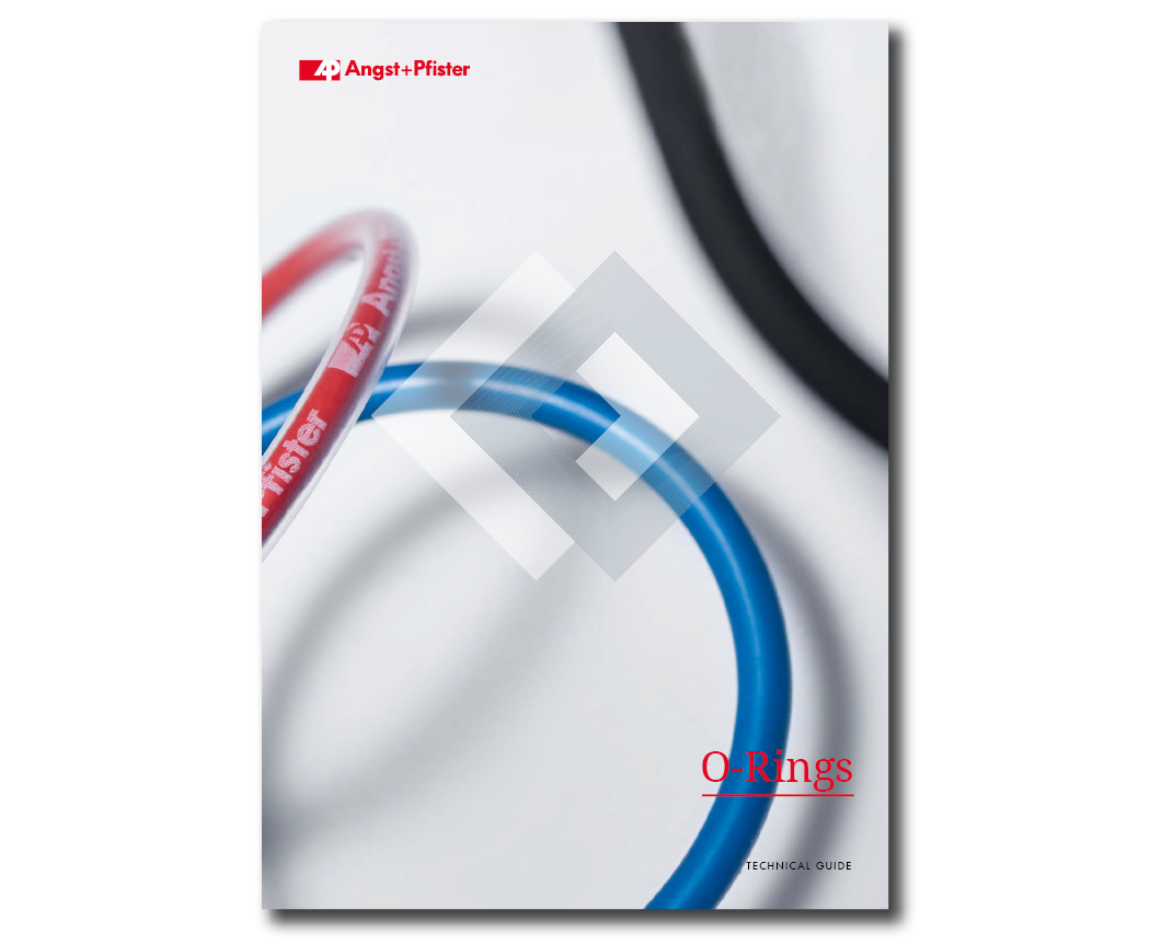
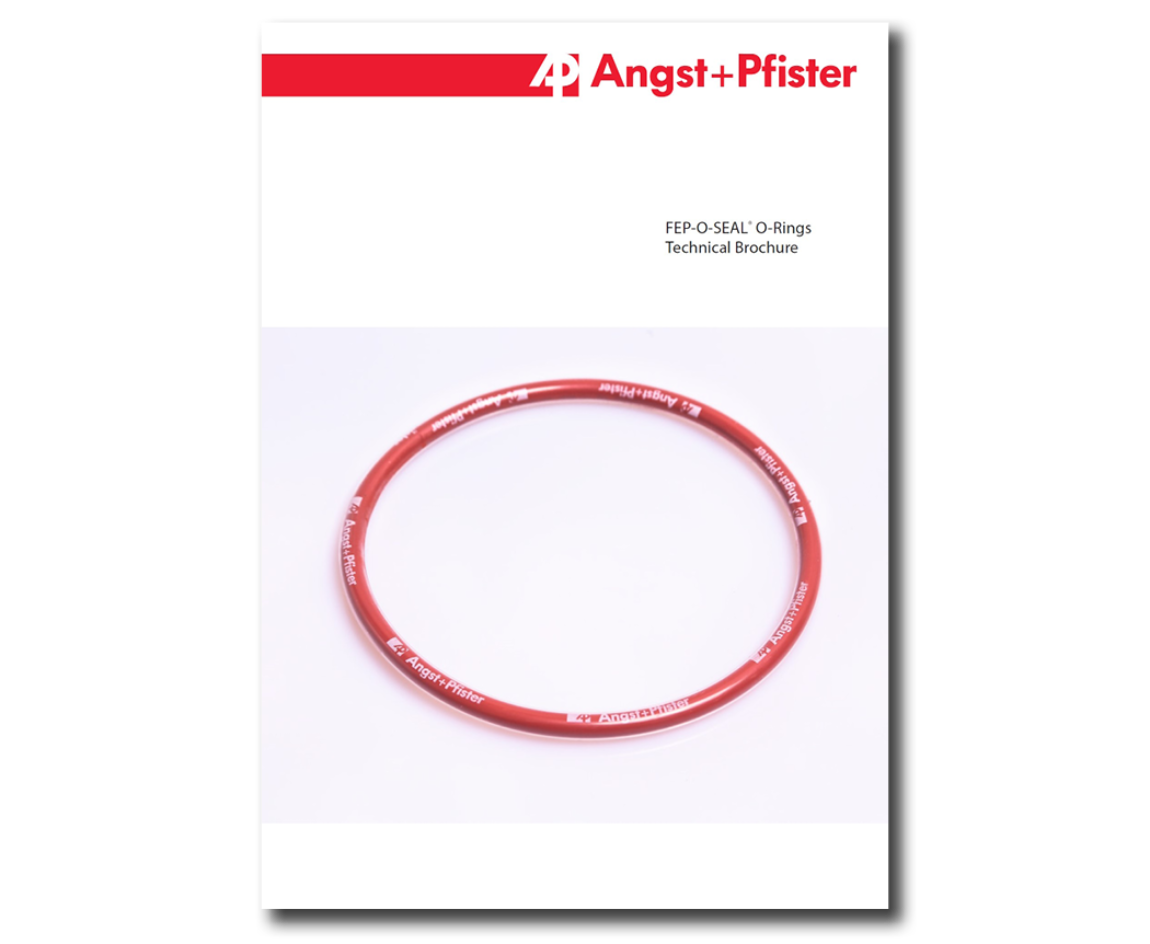