Driving Innovation
Shaping Success through Elastomers
Progressive elastomers are the backbone of tomorrow's sealing solutions. Our formulations are meticulously designed to not only meet industry specifications and standards but also to address the unique transformation your needs. From standard materials like NBR, HNBR, EPDM, and CR to high-performance compounds such as VMQ, FVMQ, FKM, and FFKM, we offer a diverse range of compounds engineered for excellence.
If you are interested in deeper information on our sealing compounding, click on the button below to consult our product lists.
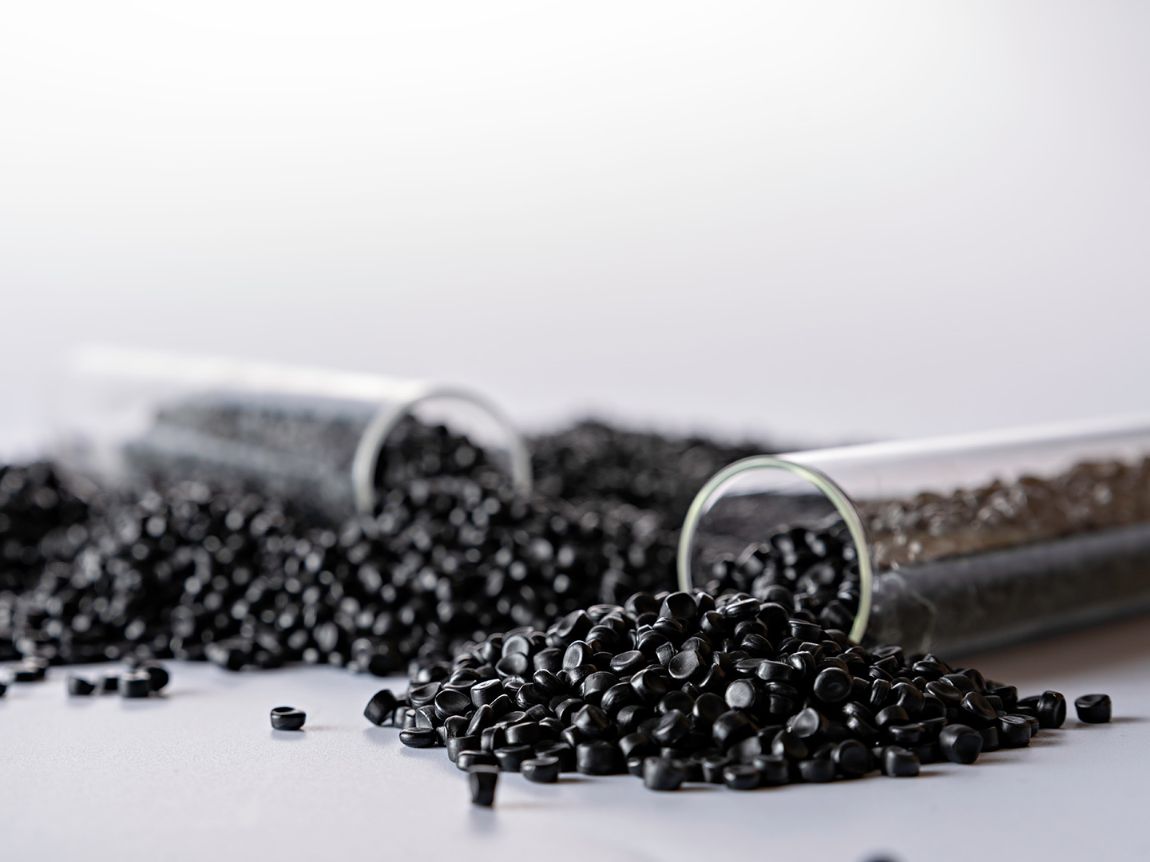
Let’s Talk about your Project!
Request a Free Consultation and Find a Perfect Solution Customized for you.
Based on our assortment we create and develop an individual solution for your application – or we even develop from scratch a high-performance part for your product to ensure quality & safety. For expert advice and customized solutions tailored to your specific needs, Angst+Pfister service offerings are your go-to resource for Elastomeric Compounds
Let's talk!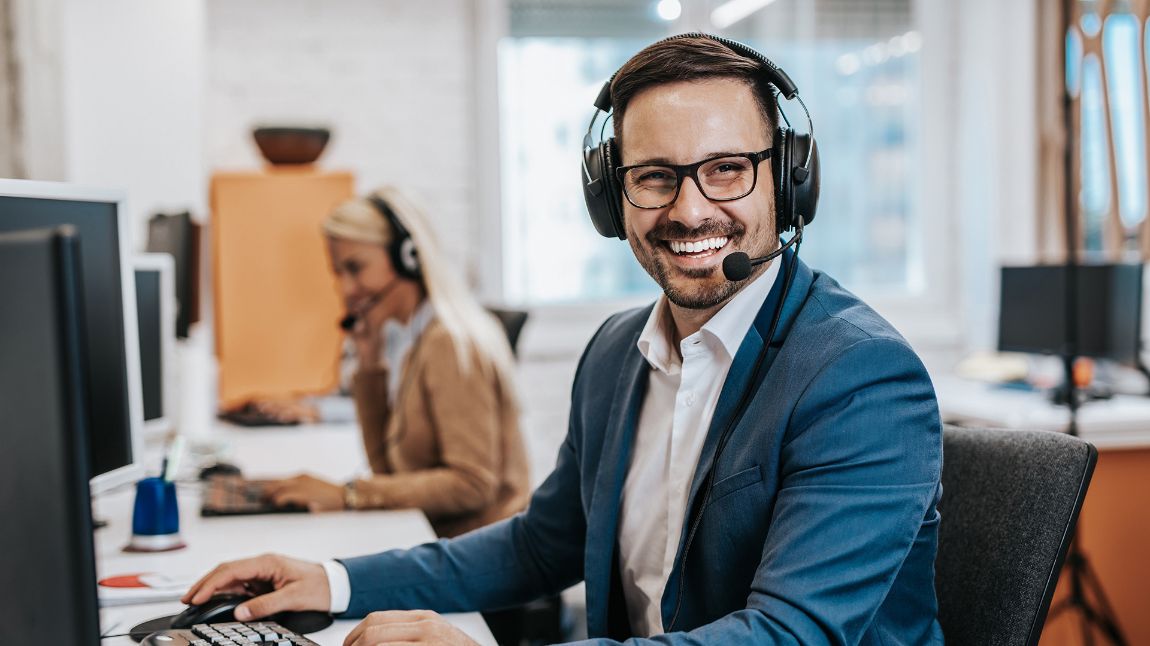